スイッチ/ボタンの反復の話です。
スイッチ/ボタンを押している状態は、クレーター電流、25A程度(溶接棒2.4)です。
スイッチ/ボタンを離している状態は、溶接電流です。板厚が3mmくらいで80から160Aくらいでしょうか。反復なので溶接電流はスイッチ/ボタン調整なので範囲は広いす。
「(ボタンを押さずに)溶接電流で進む」ことが多いのですが、「(ボタンを押して)クレータ電流/25Aで進む」こともあります。これは溶接電流が低めか高めかによって変わります。
溶接電流が比較的、低い場合はスイッチ/ボタンを離して、溶接電流で進む。よってスイッチ/ボタンを押している/25Aで冷やす時間が少ない。
溶接電流が比較的、高い場合はスイッチ/ボタンを押してクレータ電流/25Aで進む。溶接電流はほぼ一点で一瞬。よってスイッチ/ボタンを押している/25Aの時間が長い。
溶接電流が高いのであっという間に溶ける。そのため進むスピードを相当に早くないと裏波が加熱し過ぎで形は重力まかせになる。だから、スイッチ/ボタンを押して冷やす時間が長くなる。加熱しないようにスイッチ/ボタンを押しながら/25Aで進む(次に溶かす位置に移動)。そして、溶加棒を近づけて一瞬で溶かして溶加棒を入れて直ぐにスイッチ/ボタンを押して冷やす。キッチり冷やさないと形が変わる。
溶接電流が高くても手元で熱量を調節できる利点がある。溶接電流が低いとどうしようもない。
さて、仕事で使う場合は適正電流と電流高目のどっちが早くて、楽でしょうか?
きっと、慣れからしても前者でしょう。大多数が前者ですよね。後者の溶接電流を高くして、溶接は一点で一瞬で終わり、25Aで進むという人は少ないです。
ところで、溶接電流で進み、時たまスイッチ/ボタンを押して冷やす場合は、もう少し溶接電流を下げれば、反復なしで連続で溶接できます。JIS検定試験のように機械が近くにあり仮付け、ルート面、ルート間隔など溶接条件を自分でやる場合は溶接電流の調整をして連続ですることもあるでしょう。しかし、仕事ではルート間隔や母材の温度変化で連続でやりやすい溶接電流は変化します。姿勢によっても進むスピードも変化します。板の端で終わる場合はスイッチ/ボタンを必ず使います。ですから溶接電流を高めに設定しておいて、反復を使って状況の変化によって温度調節を手元のスイッチ/ボタンでするというのが便利で簡単、早いです。
さらに言いたいことあって。
ネバネバのステンレスとは違うよ!!!って話でもあります。鉄は冷やさなあかん!!!って話。以下がネバネバ順です。
- チタン
- ステンレス
- 鉄
- アルミ
TIG用溶接棒です。鉄とアルミだけですが、アルミは氷柱/ツララになります。ステンレスは玉状になります(写真にはありませんm(_ _)m)。
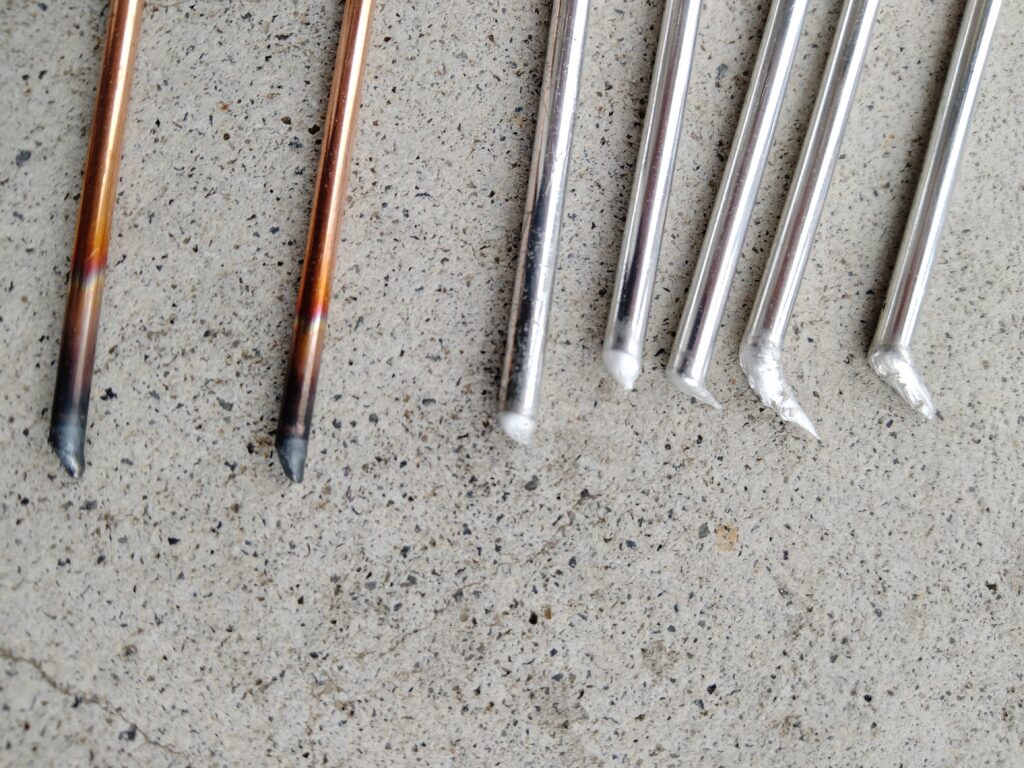
溶けた状態で流れない、形が崩れない順でもあります。TIGの場合は溶加棒を入れれずに単に温めるだけだと薄板の場合は穴が空きますが、ネバネバほどプール(溶融池)が大きくても穴になりません。ただ、アルミの場合は変な凹みや穴になります。アルミ自体(表面以外の中身)の融点は600℃ですが、酸化皮膜(表面とゆうかアルミの周り全部)の融点が2,000℃なので餅のように中だけ溶けるという状態で穴が空きにくく、シワシワの状態になってから穴になる。アルミダイキャスト/鋳物で圧力をかけるのはこのためでしょうね。
鉄は鋳物、アルミはアルミダイキャストがあるぐらいですから溶かすと流れやすい。溶けたらネバネバな材料は鋳物が無い、難しいということです。
何と、チタンやステンレスに鋳物はあります。「チタン 鋳物 難しい」で検索。「ステンレス 鋳物 難しい」で検索。本来、難しいはずなので「難しい」を入れてしまった。^^;。